Using the FIFO Method for Inventory Management
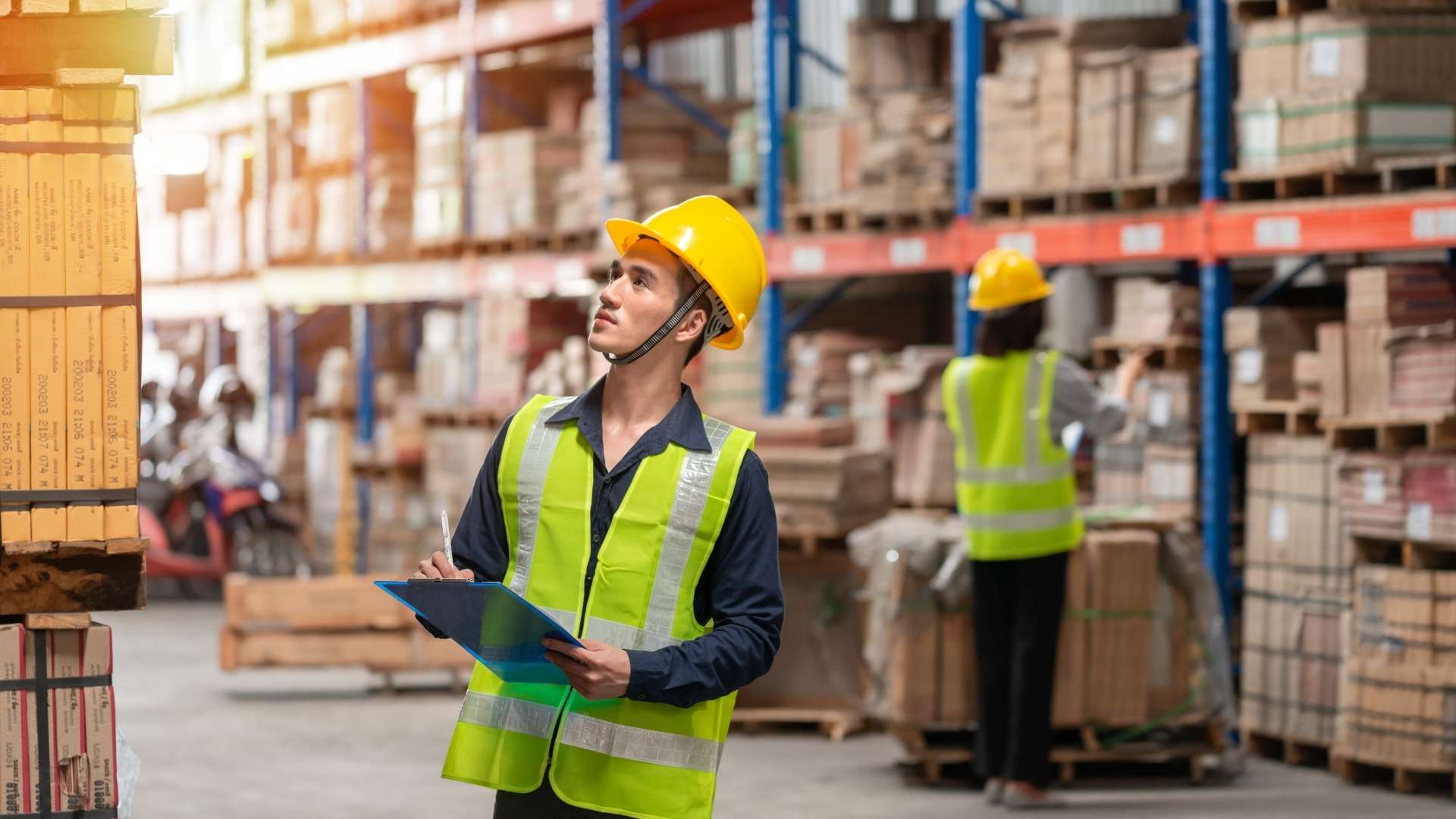
May 4, 2023
Eoin Horgan
What is FIFO?
FIFO stands for "First In, First Out", and it is a fundamental inventory management approach that is widely used across various industries. At its core, FIFO is a simple yet powerful concept: the oldest stock is the first to leave the inventory.
In other words, the products that were received or produced earliest are the ones that get shipped out to customers first.
The Advantages of FIFO
Why is FIFO so significant in the realm of inventory management?
01Accurate Cost Tracking
FIFO plays a pivotal role in calculating the Cost of Goods Sold (COGS), a critical financial metric for eCommerce businesses. By adhering to FIFO, you ensure that the cost associated with the oldest inventory is accounted for first when calculating the COGS. This approach aligns with the principle of financial transparency, helping you maintain accurate financial records.
02Reducing Waste and Spoilage
For businesses dealing with perishable goods or products with limited shelf life, FIFO is a game-changer. It ensures that products are sold in the order they were received, minimising the risk of items becoming unsellable or spoiled due to extended storage.
03Enhanced Inventory Turnover
FIFO promotes a more efficient inventory turnover rate. Older stock is sold before newer stock, allowing you to keep your inventory fresh and preventing the accumulation of obsolete products.
04Compliance with Accounting Standards
Accounting standards often recommend or require the use of FIFO, making it a prudent choice for eCommerce businesses looking to maintain financial compliance.
What is the FIFO Method?
To truly grasp the benefits and applications of the First In, First Out (FIFO) method in inventory management, it's essential to delve deeper into its core principles and how it functions within your eCommerce fulfillment set up.
Understanding FIFO Principles
FIFO, as the acronym suggests, operates on a straightforward principle: the earliest stock that enters your inventory is the first to be allocated and shipped when customer orders are received. This means that the products you acquire or produce first are the ones you dispatch first.
In a real-world scenario, think of it like the checkout line at a grocery store. The items you place on the conveyor belt first are the ones that the cashier scans and bags first. This ensures that products with the earliest expiration dates or shelf lives are the ones customers receive.
FIFO in Action
The concept of FIFO is perhaps best illustrated by the grocery store model. If you have ever visited a supermarket, you've likely witnessed FIFO in action without even realising it. When store employees restock perishable foods, they adhere to the FIFO method. Here is how it works:
Newest Items to the Back: When new shipments of goods arrive, store staff place the newest items at the back of the shelf or display rack.
Oldest Inventory to the Front: The older inventory, which was already on the shelves, remains at the front.
Customer Selection: When a customer selects a product, they typically take the item from the front, which is the oldest stock.
This meticulous arrangement ensures that inventory items are sold in the order they were received, reducing the likelihood of products expiring or going to waste. In the grocery industry, this practice not only prevents financial losses but also contributes to sustainable and responsible business operations.
FIFO in eCommerce Fulfillment
Imagine your warehouse as a virtual store shelf. The FIFO approach here involves the rotation of incoming items to the back while keeping the oldest products at the front of the warehouse shelves. When a customer places an order, your fulfilment team picks the older inventory items first, ensuring that stock moves out of the warehouse in the same order in which it was received.
This strategic handling of inventory aligns with the principles of efficiency, cost-effectiveness, and customer satisfaction. It is an integral component of modern inventory management practices that empowers eCommerce businesses to thrive in a competitive marketplace.
How FIFO Works in Practice
FIFO Shelving and Storage Systems
Efficient storage is at the heart of FIFO's success. FIFO-compliant shelving and storage systems are designed to ensure that the oldest inventory is readily accessible and used first. Here is how it works:
Rack Configuration: Warehouses are equipped with racks or shelves where products are stored. FIFO-compliant systems often feature adjustable shelves, allowing for easy reconfiguration to accommodate varying product sizes and quantities.
Product Labelling: Each product or SKU (Stock Keeping Unit) is clearly labelled with essential information such as product name, SKU code, manufacturing date, and expiry date (if applicable). This labelling facilitates easy identification and ensures that staff can distinguish between newer and older stock.
Stock Placement: Newly arrived inventory is placed at the back of the shelving unit, while existing stock is positioned towards the front. This arrangement ensures that older items are picked first, promoting a natural flow of inventory.
Order Picking and Fulfillment Using FIFO
When a customer places an order, the FIFO principle guides the order picking process within the fulfillment centre.
Order Received: The eCommerce platform registers an incoming order, specifying the products required.
Inventory Check: Warehouse staff consult the inventory management system to determine the location of the requested products.
Order Picking: The picker retrieves the required items, starting with those positioned at the front of the shelving unit—the oldest inventory. This approach aligns with the FIFO principle.
Packing and Shipping: Once all items are gathered, they are prepared for shipment, and the order is dispatched to the customer.
Overcoming Challenges with FIFO
While FIFO offers several advantages for inventory management, it is essential to address the challenges that may arise when implementing this method. Let us explore some common hurdles and effective strategies for overcoming them.
Managing Fluctuations in Demand
Challenge: One of the challenges in using FIFO is managing fluctuations in customer demand. Sometimes, demand for specific products can be unpredictable, causing variations in the pace of inventory turnover.
Solution: To tackle this challenge, consider the following strategies:
Advanced Demand Forecasting: Invest in robust demand forecasting tools and analytics to anticipate fluctuations in demand. Historical data, market trends, and seasonality should be factored into your forecasts.
Safety Stock: Maintain a safety stock level for critical items. This buffer stock can help bridge demand variations and prevent stockouts during high-demand periods.
Dynamic Reordering: Implement an automated reordering system that adjusts order quantities based on real-time demand data. This ensures that you're not overstocking or understocking items.
Dealing with Changes in Product Pricing
Challenge: In a dynamic market, product prices can fluctuate, impacting your cost of goods sold (COGS) calculations when using FIFO.
Solution: To mitigate the impact of price fluctuations, consider these steps:
Frequent Cost Updates: Regularly update your product costs in your inventory management system to reflect current market prices. This practice helps maintain the accuracy of your COGS calculations.
Adjust Pricing Strategies: If you are experiencing significant price hikes, evaluate your pricing strategies to maintain profit margins. Communicate price changes transparently with customers.
Strategies for Handling the "Bullwhip Effect"
Challenge: The "bullwhip effect" occurs when minor fluctuations in customer demand lead to significant distortions in your supply chain. This can disrupt your inventory flow, making FIFO more challenging to implement.
Solution: To mitigate the bullwhip effect, consider these approaches:
Collaborative Supply Chain: Foster collaboration with suppliers, distributors, and retailers. Sharing demand forecasts and inventory data can help align supply chain activities and reduce disruptions.
Data-Driven Decision-Making: Leverage data analytics and AI-driven tools to gain better insights into demand patterns. These technologies can help you make more accurate predictions and respond swiftly to changes.
Flexible Inventory Management: Maintain flexible inventory levels and production schedules to accommodate changes in demand. Agility in your supply chain can help dampen the bullwhip effect.
Implementing FIFO: Best Practices
Effectively implementing the First-In, First-Out (FIFO) method requires careful planning and adherence to best practices. Let us explore the key steps and strategies to ensure seamless FIFO integration.
Inventory Categorisation and Labelling
Organise Your Inventory: Begin by categorising your inventory into distinct groups based on product type, shelf life, or other relevant criteria. Clearly label each item with its purchase date and batch number. This step is essential for FIFO compliance.
Staff Training and Education
Train Your Team: Invest in staff training programmes to educate your warehouse personnel about FIFO principles and procedures. Ensure that your team understands the significance of FIFO and how it contributes to efficient inventory management.
Inventory Management Software Recommendations
Choose the Right Tools: Implementing FIFO is easier with the right inventory management software. Look for a system that supports FIFO inventory tracking and automatically adjusts stock levels based on the FIFO principle.
Regular Audits and Quality Control
Audit Your Inventory: Conduct routine audits to verify that the FIFO method is consistently followed. Check for any discrepancies between recorded inventory levels and physical counts. Additionally, maintain stringent quality control measures to ensure that older stock remains in good condition.
Effective Communication
Collaborate with Suppliers: Foster open communication with your suppliers and manufacturers. Inform them of your commitment to FIFO and request that they label products with manufacturing dates. Timely and transparent communication can prevent issues related to stock rotation.
FIFO Warehouse Design
Optimise Your Warehouse: Design your warehouse layout with FIFO principles in mind. Ensure that older inventory is easily accessible, and that newer stock is stored behind it. Implement proper signage and storage systems to facilitate FIFO picking.
Continuous Improvement
Monitor and Adjust: Regularly review your inventory management processes and adapt them as needed. Analyse data to identify areas for improvement and refine your FIFO implementation over time.
Reporting and Analytics
Utilise Data Insights: Leverage inventory reports and analytics to gain insights into your stock turnover rates and identify slow-moving items. Data-driven decision-making can help you fine-tune your inventory management strategies.
Exploring Inventory Management? Trust the Experts
Effective inventory management is crucial for the success of your eCommerce business. Whether you are considering FIFO or other inventory methods, making informed decisions is paramount.
At F4E, we specialise in eCommerce fulfillment solutions that streamline inventory control, reduce costs, and optimise your supply chain. Our team of experts are here to guide you through the complexities of inventory management, ensuring you choose the right strategy for your unique needs.
Ready to enhance your inventory practices and boost your business's efficiency? Contact us today and discover how we can tailor a solution to fit your eCommerce operations. Leave the intricacies of inventory management to the pros and focus on what you do best – growing your business.